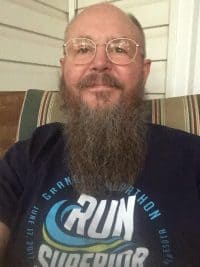
At Sawmill MD, we work for YOU!
Duncan’s years of optimization and controls experience with Harvey Electronics, Hemco, CSMI, USNR, Trident, Perceptron, and ASM enables him to identify large and small issues with the complicated electronics used in the sawmill industry. He can quantify the existing performance level of your optimization and control systems, and then suggest and implement changes needed to enhance the systems’ performance.
Using years of experience in development, production and widely varied applications, an operational assessment of optimizer systems will expose subtle faults in calibration, parameters, alignment, etc. that will improve your recovery. It is not that your technical people can’t identify issues – it is often more a matter of a fresh set of eyes focusing on a particular machine center. Understanding both machines and computers puts Sawmill MD in a strong position to make a profitable impact on your manufacturing facility.
Optimization Reviews and Equipment
Over the years Sawmill MD has provided optimization and operational consulting, and equipment, to a variety of customers, and has solved some serious issues.
Optimization Review and Tune-up for Potlatch Bemidji
Potlatch Bemidji, MN engaged Sawmill MD to do an optimization review and tune-up on the primary breakdown (Perceptron), edger (Hemco), and trimmer (Perceptron) systems. This effort resulted in financially significant improvements in the operations of the facility.
Optimization Audits for Harrigan Lumber and McShan Lumber
Sawmill MD has performed optimization audits at Harrigan Lumber in Monroeville, AL., Griffin Lumber in Cordele GA, and McShan Lumber, McShan, AL. These engagements were to evaluate the performance of the Hemco/CSMI trimmer / edger optimizers, to make mechanical adjustments that markedly improved scanning in the trimmer & edger lines and to tune-up the optimization system. The results of these projects were significant quality improvements, and the overall improvement of the optimization systems. Sawmill MD’s engagement with these and other facilities are ongoing, and include phone support, on site support, staff training, and system upgrades.
TR Miller Log Bucking Study
Sawmill MD was engaged by the mill management at TR Miller, Brewton, AL to perform a log bucking study. The scope of this project began with the evaluation of both the mechanical and electronic portions of the log bucking system. The task assigned is to advise mill management on the status of the log bucking line, and to make recommendations for the improvement in the efficiency of the bucking system. Sawmill MD discovered that the optimizer was not measuring diameter accurately, and worked with the vendor to correct these errors. Once that was accomplished Sawmill MD archived a large portion of data for analysis, and ran multiple simulations with their data. Sawmill MD used a PowerPoint presentation to show the results of the analysis, and their recommendations to the management of TR Miller. The results from this effort has led to additional tasks that the customer has engaged Sawmill MD to work on concerning the log bucking system.
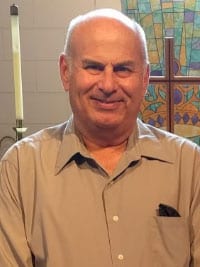
Financial and Administrative Services
Sawmill MD also provides financial and administrative services to include: identification of capital requirements, insurance review, financial system review and upgrades, forecasting, risk and vendor management. The time that Mike spent in sawmill management positions at J.L. Sizemore Sons Lumber Co., and New South, Graham NC compliments the time that Mike has had with Kockums, CSMI, USNR, and ASM on the equipment manufacturing side of the sawmill industry.
The ability to understand the production flow, equipment maintenance, staff technical capabilities, information systems, and the financial impact of management decisions allows Sawmill MD to be a full service sawmill-consulting firm. An information system review will identify the key measurements needed to manage the business. Sawmill MD’s ability to simplify and quantify financial and operational information systems will bring additional pertinent information to your management team that will allow them to make the “right” decisions based on easily attained information. The goal is to have your business optimize production to maximize profits by empowering you and your staff with the information needed to succeed.
The project management capabilities of Sawmill MD can range from project conception to final equipment commissioning. Our contacts in the industry allow Sawmill MD to work directly with vendors on your behalf to solicit bids, negotiation equipment purchases including highly favorable terms and conditions, hiring equipment installation contractors, and managing the start-up of the project. Sawmill MD has the hands-on experience to hold the machinery manufacturer and installer accountable in terms of price, performance, and warranty. We have extensive experience with identifying the potential for upgrades to your existing equipment that will maximize your return. This includes evaluation of minor changes to the equipment as well as project justification for new machine centers. Production improvement analysis along with financial justification establishes the proper level of investment for each project. Sawmill MD can put the package together to take to your financial institution. Sawmill MD also has contacts with financial institutions that may be able to help with short and long term capital requirements.